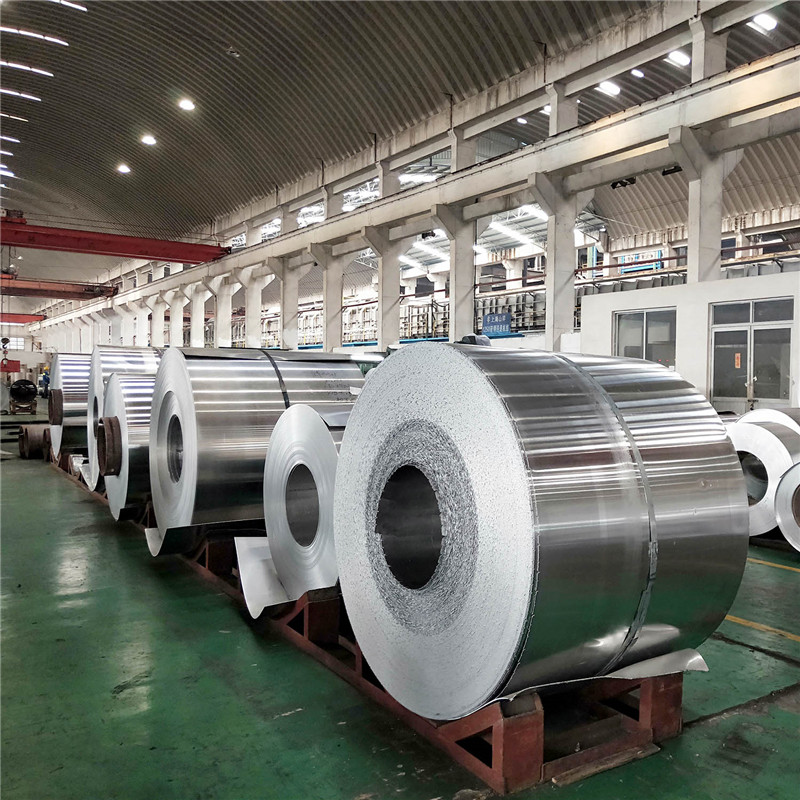
Aluminum Extrusion vs. Injection Molding: Which is Right for You?
As a manufacturer, choosing the right production method is critical to the success of your product. Two popular methods for creating custom parts and components are aluminum extrusion and injection molding. Both methods have their own advantages and disadvantages, and understanding which one is right for your product is essential. In this article, we will compare aluminum extrusion vs. injection molding and help you decide which one is best for you.
What is Aluminum Extrusion?
Aluminum extrusion is a manufacturing process that involves heating aluminum billets and forcing them through a die to create a specific shape. The result is a lightweight, strong, and versatile material that can be used in a variety of applications. Aluminum extrusions are ideal for products that require high strength, low weight, and corrosion resistance.
What is Injection Molding?
Injection molding is a manufacturing process that involves injecting molten material into a mold cavity to create a specific shape. The process can be used to produce large quantities of parts quickly and efficiently. Injection molding is ideal for products that require high precision and intricate shapes.
Advantages of Aluminum Extrusion
Cost-effective for large and simple parts
Aluminum extrusion can be a cost-effective method for producing large and simple parts, such as heat sinks or framing components. The process involves minimal tooling costs and can be used to produce parts in high volume.
High Strength-to-Weight Ratio
Aluminum extrusions have a high strength-to-weight ratio, making them ideal for applications that require high strength and low weight. They can be used for everything from body panels to suspension components, and everything in between.
Corrosion Resistance
Aluminum extrusions are highly resistant to corrosion, making them ideal for use in applications where exposure to the elements is common. Unlike steel, aluminum does not rust or corrode, which can lead to longer-lasting components and reduced maintenance costs.
Advantages of Injection Molding
High Precision and Intricate Shapes
Injection molding can make parts that are very precise and have complicated shapes. This makes it perfect for products that need tight tolerances and complicated shapes. It is also ideal for producing parts with multiple features or components.
Cost-effective for Small and Complex Parts
Injection molding can be a good way to make small, complicated parts like gears or housings at a low cost. The process makes little waste and can be used to make a lot of parts at once.
Wide Range of Materials
Injection molding can be used with a wide range of materials, including thermoplastics, thermosets, and elastomers. This makes it a great way to make parts with different properties, such as being flexible or resistant to chemicals.
FAQs about Aluminum Extrusion vs. Injection Molding
What is the main difference between aluminum extrusion and injection molding?
The main difference is the manufacturing process. For aluminum extrusion, aluminum billets are shaped through a die, while for injection molding, molten material is injected into a mold cavity.
Which method is more cost-effective for large parts?
Aluminum extrusion is generally more cost-effective for producing large and simple parts.
Which method is more cost-effective for small and complex parts?
Injection molding is generally more cost-effective for producing small and complex parts.
Which method is better for parts with intricate shapes or tight tolerances?
Injection molding is better for producing parts with intricate shapes or tight tolerances.
Which method is better for producing parts with different material properties?
Injection molding is better for producing parts with different material properties, as it can be used with a wide range of materials.
Choosing the right production method is essential for the success of any product. By comparing aluminum extrusion vs. injection molding, manufacturers can determine which method is best suited to their needs. Aluminum extrusion is ideal for producing large and simple parts with high strength-to-weight ratios and corrosion resistance, while injection molding is better for producing small and complex parts with intricate shapes and different material properties. Understanding the advantages and disadvantages of each method can help manufacturers make informed decisions and achieve their production goals efficiently and cost-effectively.